- Answering the call to fight COVID-19.
- Quidel Sofia® 2: Rising to the challenge in a time of urgent need.
- All hands on deck to ramp production of the Sofia® 2 analyzer.
- The key to rapidly scaling Sofia® 2: collaboration and communication.
- Meeting a critical need for Sofia® 2 SARS Antigen FIA test devices.
Solution Spotlight
Customer
Solutions
- Manufacturing
- |
- Supply Chain Solutions
Product
Markets
- Healthcare / Life Sciences
Answering the call to fight COVID-19.
Quidel, a leader in diagnostic healthcare, needed to rapidly scale production of the Sofia® 2 fluorescent immunoassay analyzer to support increased demand for point-of-care testing devices used in the fight against COVID-19. They called on Plexus to help make it happen.
Quidel Sofia® 2: Rising to the challenge in a time of urgent need.
At the height of the COVID-19 pandemic, one question was on much of the world’s minds: “What can we do to help?” For Quidel, a manufacturer of diagnostic devices for the healthcare industry, the answer was simple — get more of the Sofia® 2 Fluorescent Immunoassay Analyzers out to the world, making as many Sofia® SARS Antigen FIA tests available as possible.
But a simple answer isn’t necessarily a simple task.
As COVID-19 was spreading across the globe, the surging demand for medical devices, supplies and protective equipment was squeezing healthcare supply chains. Shortages began cropping up in all areas of the global supply chain. Which means the medical and diagnostic devices that were so crucial to identifying, treating and fighting COVID-19 — devices like the Quidel Sofia® 2 — would only become more difficult to produce.
It was against this backdrop of increasingly urgent need and critical supply shortage that Quidel turned to Plexus to help get their potentially life-saving Sofia® 2 into as many frontline hands as possible. Together, we were all in — ready to do whatever it would take to mobilize our resources, build the necessary supply chain and design the manufacturing process to ramp up from hundreds of Sofia® 2 per week to thousands, in as short a time as possible.
The Quidel Sofia® 2 Fluorescent Immunoassay Analyzer is a small bench-top instrument that delivers fast, highly accurate, objective and automated results you can rely on in 15 minutes or less with Advanced Result Technology. It would play a critical role in providing much-needed, rapid COVID-19 tests at the point of care.
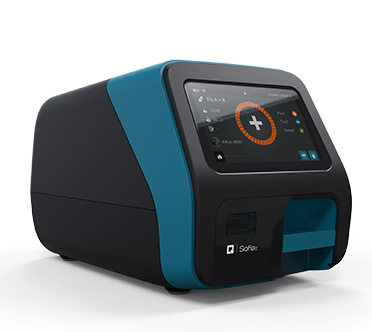
The Plexus team was fully invested in the cause to help Quidel bring the Sofia® 2 antigen test analyzer to the market as quickly as possible.
All hands on deck to ramp production of the Sofia® 2 analyzer.
Quidel and Plexus had already built a solid, successful partnership through an existing design and engineering engagement. When Quidel reached out to us with the challenge to scale Sofia®2 so quickly, we were already working from a strong foundation. What’s more, our two companies shared the same values, goal and sense of purpose — to help create the products that build a better world, and enhance the health and well-being of people around the globe. We were one team, all rowing the same direction, with complete buy-in from top leadership and throughout every level of our organizations.
Though manufacturing the Sofia® 2 was new to us, coming up with solutions to help solve a partner’s problem is not. Our manufacturing team immediately understood the importance of this project. The close integration of our engineering and manufacturing solutions made it possible to set up production lines quickly, while also prioritizing the safety of our teams during the height of the pandemic. Plexus had already put stringent health and safety protocols in place, and we were able to seamlessly implement the new workflow in a way that would remove much of the risk of COVID-related downtime. This allowed us to maximize operational efficiency and accelerate the production process.
At a time when there was severe disruption to healthcare supply chains, Plexus was able to collaborate with and complement the Quidel team to ensure that critical components got where they needed to be quickly. Our supply chain team brought decades’ worth of experience and relationships to the table, working as an extension of the Quidel team to help solve complex supply chain challenges. This alignment of resources empowered the team to overcome the most difficult roadblocks and celebrate project success together. For Quidel, this level of agility and collaboration made it possible to manufacture the Sofia® 2 at an increased rate — always with an eye on the ultimate goal, to help save lives.
The key to rapidly scaling Sofia® 2: collaboration and communication.
The partnership was up against the clock. There were real people counting on these devices every minute. This timeline was not set internally to meet business goals, but was driven externally by how fast the COVID-19 virus was spreading. Quidel’s Sofia® 2 rapid test devices needed to get to market, and fast.
To achieve this, Quidel and Plexus established a leadership steering committee that met weekly to discuss progress and find solutions to project challenges. It was a clear demonstration of the communication and integration of our two companies at the leadership level. And it set the precedent for how the project and manufacturing teams would collaborate throughout the process.
Even in this fast-paced environment, it was essential that the daily project team was aligned for success. To ensure a seamless integration of the two teams, a transition team managed timeline and leveraged communication best practices across the multiple workstreams involved in bringing the Sofia® 2 to market. This included establishing clear benchmarks that we needed to meet before moving on to the next project activity. The Quidel and Plexus teams also met daily to update the project plan in real time based on recent progress. This ensured that the project would be completed in an accelerated timeframe while meeting quality and safety standards.
“The Quidel Team was first to market and quick to ramp production of our Sofia® SARS rapid antigen test strips to detect transmissible levels of coronavirus in 15 minutes, but we needed to bring our Sofia® 2 fluorescent immunoassay analyzer capacity to a scale commensurate with the enormous testing volume and the urgent public-health need,” said Douglas Bryant, president and CEO of Quidel Corporation. “We were in a war with COVID-19, and we needed a force multiplier.”
“We found our ideal partner in Plexus,” Mr. Bryant continued. “The Plexus Team worked with us in lockstep — from planning and procurement to manufacturing and quality control. Their entire operation was safe, secure and swift. The excellence and dedication Plexus brought to the effort enabled Quidel to better fulfill our mission to democratize access to accurate and affordable COVID-19 testing and support our healthcare heroes on the front lines of the pandemic fight.”
The industrial operators at our Neenah, Wisconsin, facility developed a clear plan to maximize productivity and decrease downtime. Each step of the manufacturing process had owners responsible to keep manufacturing efficient. Manufacturing engineers knew the importance of setting up the line to adhere to COVID-19 protocols. Quality engineers made sure that every device met stringent standards. And industrial operators understood the importance of reducing unnecessary machine or operational downtime.
With Quidel’s device expertise and the proven manufacturing and supply chain solutions Plexus brought to the table, we were able to form a highly successful collaboration. And the alignment of purpose was the key to it all. Healthcare professionals were depending on these devices to provide patients with accurate COVID-19 test results to determine the appropriate care. Every team member understood the urgent need to make this project a success.

We were in a war with COVID-19, and we needed a force multiplier. We found our ideal partner in Plexus.
Douglas Bryant • President and CEO, Quidel Corporation
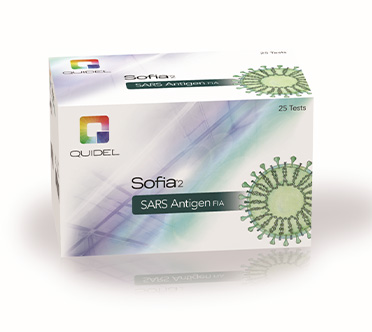
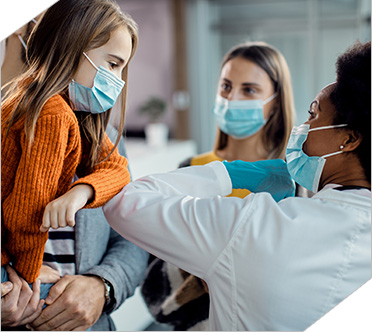
Meeting a critical need for Sofia® 2 SARS Antigen FIA test devices.
Through close collaboration, clear communication and efficient operations, we were able to answer the question, “What can we do to help?” With lives depending on quick, accurate COVID-19 test results, the Quidel and Plexus partnership made every effort to get the Sofia®2 into the hands of the healthcare workers who needed them most. And the work our teams accomplished together has helped set the stage for a fast, smart and highly collaborative response whenever a similar need should arise.
The proof of the impact we were able to make is undeniable — scaling to produce tens of thousands of Sofia® 2 analyzers that made possible millions of individual COVID-19 tests. This is the kind of work the Plexus team takes pride in. We’re thankful to Quidel Corporation for their partnership, and especially for the trust they placed in our team to help deliver life-saving technology to fuel the fight against COVID-19.
- Answering the call to fight COVID-19.
- Quidel Sofia® 2: Rising to the challenge in a time of urgent need.
- All hands on deck to ramp production of the Sofia® 2 analyzer.
- The key to rapidly scaling Sofia® 2: collaboration and communication.
- Meeting a critical need for Sofia® 2 SARS Antigen FIA test devices.